Moving Aluminum Production Into the Future
Episode 2 of our blog series explores aluminum's vitality to the clean energy transition
Annie Sartor, Aluminum Campaign Director, Industrious Labs
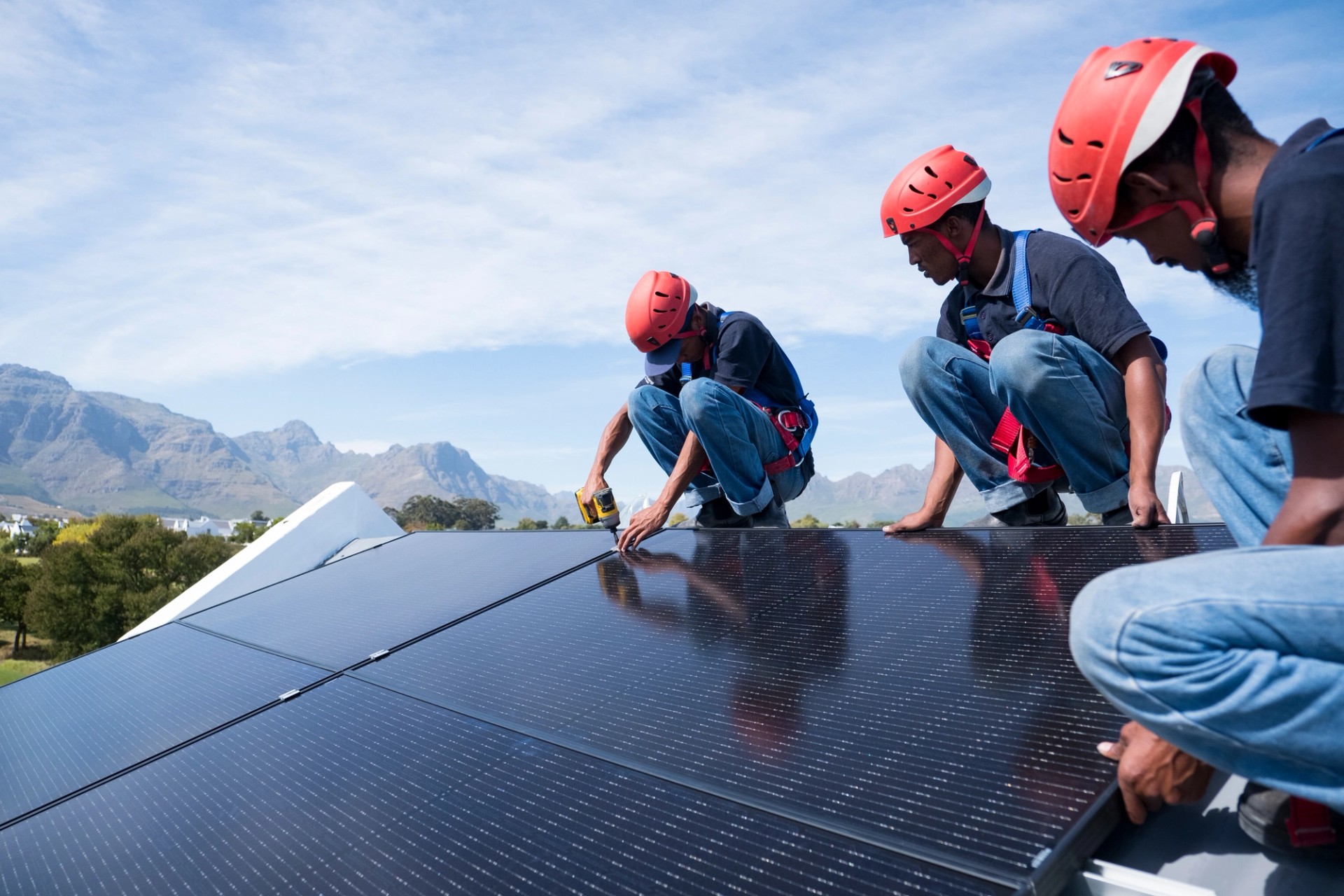
"Modernizing and revitalizing the U.S. aluminum industry goes hand-in-hand with decarbonizing. Our ambition is to do all three of these things at once, and sustainable aluminum is the key."
Think of all of the ways we rely on modern technology to make our lives easier. Our smartphones keep track of our calendars and appointments so we don’t need to write them out by hand, and the advent of online banking has allowed us to eliminate the need to pay our bills by mail or take a trip to the bank.
While the rest of us have moved into the 21st century, much of U.S. aluminum manufacturing is stuck in the past. Many of the facilities are antiquated, and their production processes rely on the same fossil fuel energy resources, like coal, that they did a century ago. It’s the equivalent of using an abacus to do calculations when we’ve got smartphones in our pockets.
Aluminum is overdue for an upgrade. The good news is that technology upgrades that can produce sustainable aluminum are here, and they’re already being used in other countries. Sustainable aluminum is made using modern production methods that eliminate or greatly reduce carbon emissions and air pollution, and are powered by clean energy resources like wind, solar, and geothermal.
Emissions Breakdown Right now, legacy production processes of aluminum release harmful chemicals and gas emissions into the atmosphere (as reported in the EPA’s National Emissions Inventory), including carbon dioxide (CO2), carbon monoxide (CO), sulfur dioxide (SO2), and hydrogen fluoride (HF). Reducing these emissions is where modern technology becomes such a huge advantage. Of the operating U.S. smelters making primary aluminum, however, the majority use outdated technology and burn fossil fuels like coal and gas for electricity. Aluminum needs a lot of electricity—it accounts for up to 40% of the total production cost. Because the cost of fossil fuels have soared since the start of 2022, the U.S. aluminum industry has been forced to reduce operations, cut jobs, and close plants.
Global aluminum production emitted about 1.1 Gt of greenhouse gas emissions in 2020, contributing 2% of global emissions. A typical ton of aluminum made with zero-emissions electricity like hydropower releases about 4 tons of carbon emissions, mainly due to emissions resulting from alumina refining and the smelting process. By comparison, a ton of aluminum made with coal-fired electricity releases up to 20 tons of carbon emissions, more than five times more. Major companies like Apple are starting to demand cleaner aluminum. Apple has partnered with Alcoa on a new test facility in Canada that eliminates carbon emissions from the smelting process itself—not just from the electricity generation. Soon, it will be possible to make 100% sustainable aluminum if a smelter is powered by clean electricity.
Primary versus Secondary Aluminum Modernizing and revitalizing the U.S. aluminum industry goes hand-in-hand with decarbonizing. Our ambition is to do all three of these things at once, and sustainable aluminum is the key. Many aluminum buyers in the U.S. are already moving in this direction by ensuring their manufacturing and supply chains are also low-carbon. Purchasing recycled aluminum—also known as secondary or scrap-based aluminum—is one of those methods. Primary aluminum, in comparison, is newly manufactured aluminum (ultimately deriving from mined ore). Secondary aluminum uses much less electricity to produce, and because it is a “recycled” product, has much lower emissions and less pollution associated with its production. Keep in mind, the largest purchasers of primary aluminum are secondary aluminum producers; they source primary aluminum due to economic and supply chain reasons to meet demand and to satisfy material specifications. In fact, primary aluminum can represent a significant fraction of secondary aluminum, depending on the end use product.
The good news is many industries are working to use as much secondary aluminum as possible in their products—like solar panels, electric vehicles, and packaging—as a key way to meet climate commitments, and secondary production is growing. However, primary aluminum demand is still expected to increase by 40% by 2050 to meet global needs, for use in specific applications, and in producing secondary aluminum.
Historical Aluminum Consumption and Projected Demand
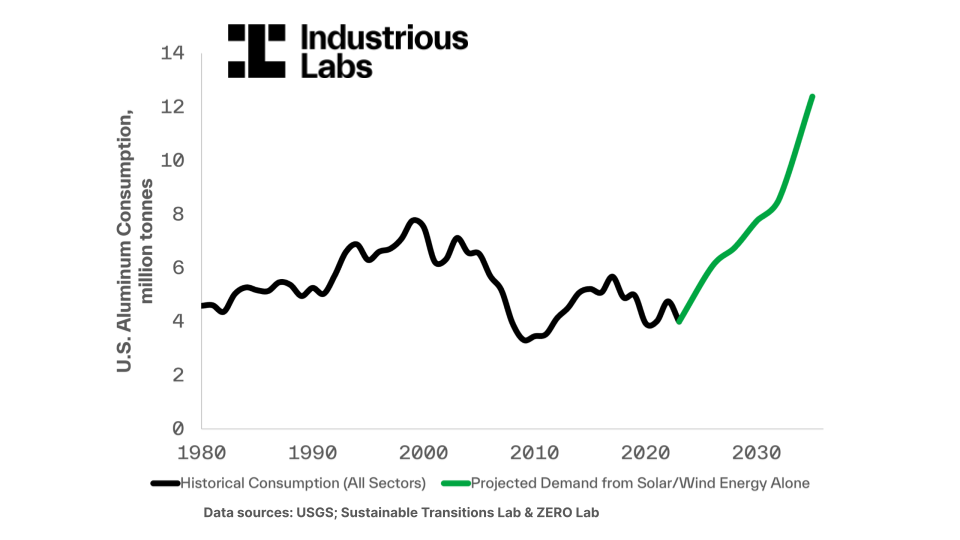
This table presents historical consumption and projected demand for all aluminum, indicating a spike in demand for aluminum for wind and solar by 2035.
Moving into the clean energy transition So, successfully decarbonizing, revitalizing, and modernizing the industry means we need to start by cleaning up primary production first. We have an enormous opportunity to restore the industry, re-shore jobs, and protect our climate. As the clean energy transition accelerates and demand for solar panels, heat pumps, electric vehicles, and transmission lines skyrockets, global use of aluminum is forecasted to soar 80% by 2050. If we don’t act now to modernize U.S. primary aluminum production, greenhouse gas emissions will grow similarly, prolonging outdated, harmful practices that will accelerate the climate crisis. We have better technologies for making the aluminum we’ll need now and in the future. Let’s leave fossil fuel-based production where it belongs: in the past.